*For better visibility open pictures in new window.
Item DEV001 is min-max planned item with minimum quantity 20
If the quantity of DEV001 goes below 20 in FG subinventory then, user is going to take DEV001 from RM subinventory where huge stock for this item is maintained..
For this create an item in the Item Master. In the General Planning tab, selects the Inventory Planning Method as Min-Max. and source type as Sub-inventory.
In the Planning tab for the FG subinventory, specifies that the item DEV001 is Min-Max driven whenever it resides in FG. And whenever the quantity falls below the Min Qty of 20 in FG, it will be time for Min-Max to trigger replenishment.
In the Order Modifiers tab an opportunity is there to specify a Fixed Lot Multiple of 15. This implies that the quantity for replenishment will be suggested (calculated by the Min-Max algorithm) in multiples of 15. Minimum 30 items has to be ordered and maximum of 150 at a time.
There can be multiple order lines to reach Max Qty 400 (say 150+150+100). But the Fixed lot Multiple is 15, so order can’t be of 100 qty (100 is not a multiple of 15). Hence max level of 400 can be reached by orders of 150 +150+105 qty (Total 405).
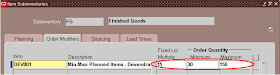
Finally, in the Sourcing tab, mention that RM will be the sourcing subinventory.
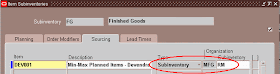
Now checkout the on-hand for DEV001 in FG.
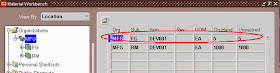
As the on-hand in FG for DEV001 is just 5 i.e. below minimum level of 20, it’s time to trigger replenishment.
The only task that is left is to run the Min-Max Planning report. This report serves to highlight items that need replenishment and also suggests the replenishment quantity based on the setup.
Unlike most reports, the Min-Max Planning report can also trigger the replenishment process. This means creating Pre-Approved Move Orders to fulfill the suggested replenishment quantity.
To launch the replenishment process, run the Min-Max Planning report with the parameter Restock set to Yes
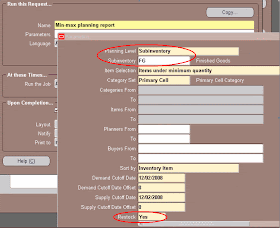
The O/P of this report shows that Reorder Quantity as 405. This figure matches with the calculation given above. That indicates we are on the right track so far. As the report has Restock=Yes it must have generated pre-approved Move Order.

Search for the Move order created:
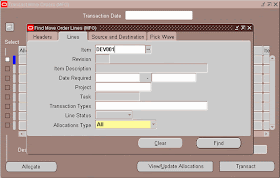
Here again above calculation proves it self. There lines got created to reach max qty level of 400.
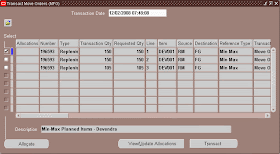
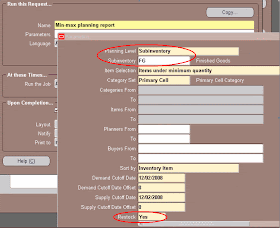
The O/P of this report shows that Reorder Quantity as 405. This figure matches with the calculation given above. That indicates we are on the right track so far. As the report has Restock=Yes it must have generated pre-approved Move Order.

Search for the Move order created:
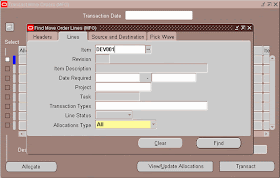
Here again above calculation proves it self. There lines got created to reach max qty level of 400.
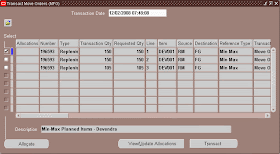
Now just allocate (click on Allocate button) material for the lines and simply transact the same. If the item on line is serial/lot controlled the allocation must be done by clicking button View/Update Allocation button.
After Transact Move Order material must have reached to destination i.e. in FG sub-inventory.
Just checkout this:
Here the cycle gets completed….
Now user can consume material form FG sub-inventory and the replenishment will keep happening whenever stock comes below the specified level.
Similarly we can follow the cycle for the items which are purchased by selecting supply type as Supplier and so on….
Another wonder full article on Min Max planning is ... https://www.apps2fusion.com/apps/apps-training/801-min-max-plan-r12 and here example is of replenishing from different inventory organization
Keep practicing…. Keep blogging….
Hi Dev,
ReplyDeleteThis is a very good article I must say... also I must appreciate your style to make articles...
thanks for that...
Keep it UP
Pankaj
Hi Devendra,
ReplyDeleteReally Awesome docs..
Tushar
Hi Dev,
ReplyDeleteThe content, presentation and flow are really good. Keep'em coming
Regards,
Kartik Krishn
Hi Devendra,
ReplyDeleteThanks for the article. I have a doubt here
If the Item sourcing is Supplier and I generate the Min Max Report with Restock set to "Yes", will the system generate PRs for the item or anything other than that. Please reply.
Regards,
Pavan
by reading this doc only i understood about order modifiers tab.....thank you very much.....really its good
ReplyDeleteThank you so much for the post. What if your RM inventory doesn't have enough stock to fulfill move order? When you run the MRP, would it generate planned order for shortage?
ReplyDelete1. If RM does not have enough stock to fulfill then the Move order can not be transacted competently. You can wait till stock is available or u may transact partial Qty on Move Order and then later on when more stock comes to RM you may transfer rest of the qty.
ReplyDelete2. MRP and Min-Max planning are two different material planning methods which can work independently. As far as generation of Planned Order after running MRP is concerned, it can be generated provided sourcing setup is done properly.
Thanks
Devendra Gulve
how can i auto create internal order based on Min-Max qty, any suggested API or work around its urgent,
ReplyDeleteCan Anyone suggest me how to auto create Internal Requisition based on Min-Max qty and suggestion which API and work around, plz you suggestion are valuable to me.
ReplyDeleteMy min max planning report is not showing anything, what to do? I think I pre-approved move order that is the problem or something else??
ReplyDelete