In today’s environment where lead times are often only a matter of 24 hours, many companies want to create a specific supply order linked to each customer order and they want these supply order created as soon as the customer orders have been booked. These companies want to have the supply order “hard pegged” to the customer order that it is supplying, and once the supply reaches the warehouse they do not want it inadvertently taken by another order or demand. They also need visibility to where the Sales Order line is in the process at all times, so they can answer customer service inquiries. We call this process ‘Back-to-back orders’, indicating that the Sales Order and the supplying Purchase Order are very closely linked, often where one PO is tied to one Sales Order.
Key Business Drivers
Lower inventory cycle time and cost
Link supply to specific demand
Can offer a variety of product to customer
Used heavily in contract manufacturing environment where the product is standardized and the company plans to focus more on product design rather than manufacturing.
Create a B2B item :
In the Order Management tab, check the Assemble to Order flag (ATO).
In the Purchasing tab, enter a value in the List Price field (in this demo it is 100).
In the Work in Process tab, make sure the Build in WIP flag is checked.
In the General Planning tab, set the Make or Buy flag to Buy.
Save, and assign to Organization M1
Note: the ATO item attribute is checked as the B2B process utilizes the ATO process of the workflow. However, the item is not manufactured in WIP, and instead is a 'Buy' item that is replenished by a supply order in PO. Hence the item may also be called an ATO Buy item
Assign the item to the price list
Make sure the following periods are open:
Inventory Accounting Periods
Purchasing Periods
GL Period
Create a sales order with Order Type Mixed and enter the B2B item in the lines for any quantity.
Book the order. Note down the Order Number. Booking will progress the order line to workflow activity “Create Supply Order – Eligible”.
Place cursor on the line and go to Actions > Progress Order. Select Create Supply Order - Eligible to progress the workflow of the line.
This will insert the data into Requisition Interface table as well as progress order line workflow to SHIP_LINE activity.
Go to Purchasing > Reports > Run and run the concurrent program Requisition Import with the Import Source parameter = CTO (or blank). Leave the other parameters as default. The concurrent program can also be run from OM > Orders, Returns > Requisition Import
Go to Purchasing > Requisitions > Requisition Summary.
In the Find Requisitions window, enter requisition number found in the previous step and click on Find.
Verify that the status is Approved Requisition must have status APPROVED as we ran Req. Import with Requisition approval initiation= Yes
Go to Purchasing > Autocreate.
From Edit > Clear > Record, clear any query criteria that may be defaulted.
Enter requisition number and click Find.
Check the checkbox to the left of the line, and click on Automatic.
Enter the Supplier and Supplier site such as the following and click on Create
The Purchase Order form will automatically open with the PO that got created.
Click on the Approve button.
Click on the OK button in the Approval Documents window to approve the PO.
Note down the PO number, and verify that the status is Approved
The line status of the sales order line will now show PO-Created (flow_status_code PO_CREATED).
- Once PO got approved MTL_RESERVATION table got updated with supply_source_line_id = PO_LINE_ID and demand_soure_type = PO
Go to Purchasing > Receiving > Receipts.
Enter Purchase Order number and click on Find.
In the Receipts window, check the checkbox to the left of the line and enter
Destination Type : Inventory
Subinventory : FGI
Save the receipt.
Go to Purchasing > Receiving > Receiving Transactions Summary.
Enter the Purchase Order number and click on Find.
Click on the Transactions button.
Verify a Receive and Delivery transaction. This means that the B2B item has been received into Inventory.
Pick Release the Sales Order
.
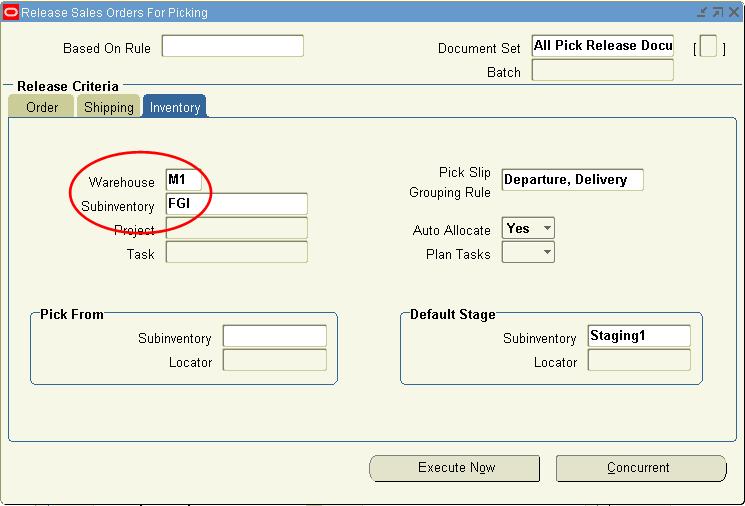
Now the Line is eligible for Shipping Activity. Ship Confirm the Order and verify the line status.
Go ahead with invoicing the Order Line/s.
In this case there will be two invoices.
One in AR which will be issues against Sales Order
One in AP which will be issued against Purchase Order / Receipt.
Managing Changes in Purchasing
- Changes to a requisition (other than requisition cancellation) will NOT be reflected in the reservation to the sales order. Therefore, it is recommended that users never change a requisition with source type CTO.
- If the PO is canceled without canceling the requisition, the reservation is transferred back to the requisition. If both are canceled, the reservation is removed. In the latter case, you can run the autocreate purchase requisition batch program to create a new requisition for sales order.
- If a partial PO quantity canceled, or the PO qty is reduced, then the reservation quantity is reduced accordingly. Again, run the autocreate purchase requisition batch program to create a new requisition for the outstanding quantity.
- Receive an Assembly: When a purchase order has been reserved to the sales order, the inventory will be automatically reserved against the sales order when you receive the purchase order.
- Once a sales order reservation to the PO has been removed (either automatically or manually), it cannot be manually re-reserved. You can manually reserve on-hand stock to the sales order or the autocreate purchase requisition batch program can pick it up again and create a new supply order along with a new reservation.
If for some business reason customer needs to cancel the PO and requisition, in such a case Cancellation of PO result in deletion of the complete record from MTL_RESERVATION table and also B2B order line workflow rewind back to “Create Supply Order – Eligible” workflow activity , also flow status code on OE_ORDER_LINES_ALL updated back to "Supply Eligible"
Now if user cancel the requisition and once again progress the workflow it result in creation of new requisition ( via requisition import) and now record in mtl_reservation table.
Also refer a White paper on Back 2 Back order. Metalink Doc ID 396951.1
*For better visibility CLICK HERE.